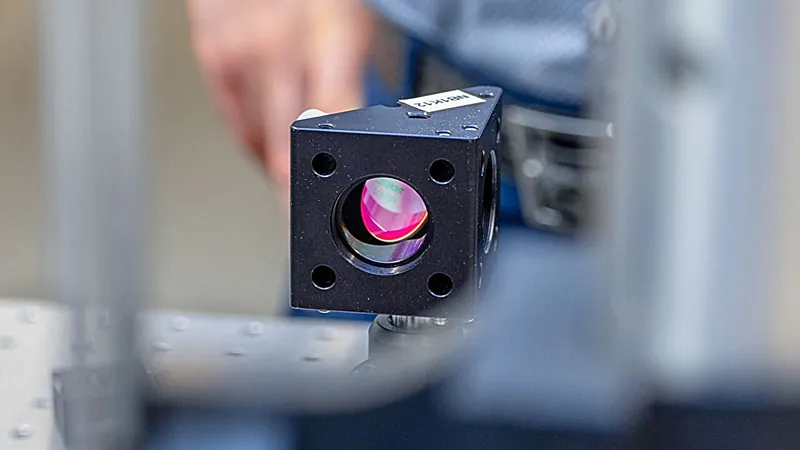
Groundbreaking Research Unleashes the Secrets of Supersonic Metal Bonding!
2024-11-07
Author: Wei
Groundbreaking Research Unleashes the Secrets of Supersonic Metal Bonding!
In a remarkable breakthrough, researchers at Cornell University have developed a cutting-edge approach to studying the dynamics of metal bonding through high-speed collisions. Utilizing a custom-built machine that can launch microprojectiles at supersonic speeds, the team has unveiled new insights into the solid-state bonding process that occurs at the atomic level when metallic particles collide. This study, set to revolutionize 3D printing and manufacturing, could have profound implications for various industries, including aerospace and energy.
The phenomenon known as solid-state bonding allows two metals to fuse without the need for extreme heat or melting, resulting in exceptionally strong atomic bonds. Although researchers have long understood the general conditions required for bonding, the intricate microstructure and material properties resulting from these high-speed impacts remained largely unexplored—until now.
In a study published in *Nature Communications*, Cornell researchers meticulously examined how bond strength and gradients develop across interfaces formed by supersonic impacts. "This research marks a significant shift in our understanding of how process, microstructure, and material properties are interlinked in impact-induced bonding," stated Mostafa Hassani, the senior author and a leading figure in the study. These findings pave the way for the reliable design of advanced manufacturing technologies that depend on these unique bonding mechanisms.
One of the most exciting aspects of this research pertains to what is known as "cold spray" or supersonic 3D printing. This innovative technique performs material production without heating the components, which not only preserves the integrity of the material but also enhances its mechanical properties compared to traditional procedures. These advantages position supersonic 3D printing as a leading solution for high-performance applications across several industries, particularly in the development of critical aerospace components.
To conduct their experiments, the researchers designed a state-of-the-art laser-induced launch platform that successfully propelled micrometer-sized aluminum particles at speeds exceeding 2,200 miles-per-hour toward an aluminum substrate. Following the high-velocity impacts, the team utilized advanced micromechanical tensile testing paired with scanning electron microscopy to analyze the bond strengths at various points along the impact interface.
Astoundingly, the study revealed that the bond strength is not uniform across the impact zone; instead, it demonstrates significant variability. For instance, the bond strength was found to be relatively weak at the center of the impact but increased rapidly, eventually plateauing towards the edges. A striking discovery was that the form of the native oxide at the interface—whether in the form of layers, particles, or debris—significantly influenced the level of bond strength. Areas with scattered oxide debris showed markedly stronger bonds, while regions with intact oxide layers were less robust.
To further comprehend the bond strength variations, the researchers crafted a predictive model based on two key elements: contact pressure and surface exposure. When a microparticle strikes the substrate, shear forces fracture the oxide layer, revealing more metal surface. This newly exposed surface is then forced into close proximity by the impact pressure, facilitating the formation of a robust metallic bond.
"This knowledge allows for groundbreaking possibilities to customize interfacial properties and engineer optimal impact conditions—such as adjusting particle materials, sizes, velocities, and temperatures—to further augment bond strength," explained Qi Tang, the lead author and PhD student involved in the study.
Moreover, the findings also shed light on preventative strategies against unwanted bonding, such as engineering surface structures to guard against contamination from supersonic impacts. This could be particularly useful for spacecraft shields and telescope lenses facing hazardous space debris.
As we embrace the era of advanced manufacturing, this disruptive research not only expands our understanding of materials science but also opens doors to innovative engineering solutions. The future of super-strong, lightweight materials is brighter than ever!