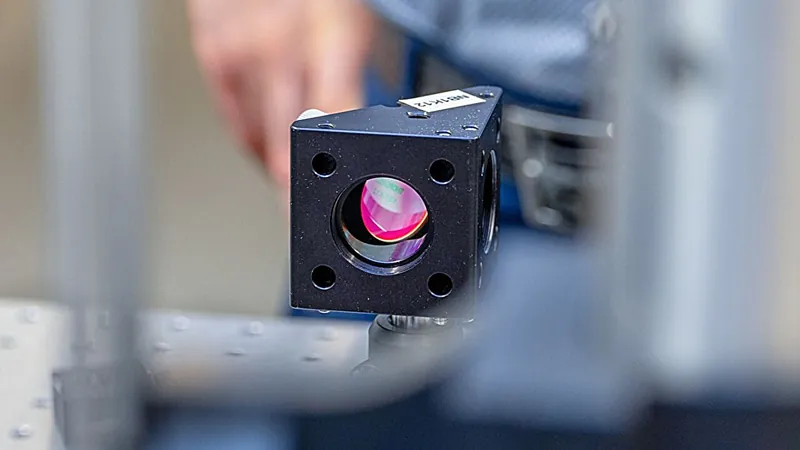
Breakthrough Research on Supersonic Microprojectiles Could Revolutionize Metal Bonding and 3D Printing Techniques!
2024-11-07
Author: Jacques
In an exciting development that could change the landscape of manufacturing, researchers at Cornell University have utilized a custom-engineered machine to propel microprojectiles at staggering supersonic speeds. This innovative research has unveiled crucial insights into how high-velocity metallic collisions can generate robust atomic bonds, which may significantly enhance various manufacturing processes, including 3D printing.
When accelerated microparticles strike a metallic surface at supersonic speeds, a phenomenon known as solid-state bonding can occur. This bonding process unites two metals on the atomic level, offering a new frontier in the understanding of material properties and microstructures resulting from these high-speed interactions. Despite a solid grasp of the conditions necessary for bonding, the specific microstructural outcomes had previously remained largely unexplored.
A detailed study published in Nature Communications highlights the remarkable variations in atomic bond strength resulting from supersonic impacts at a micrometer scale. This study not only redefines our comprehension of the relationship between process mechanics and the resulting material properties, but it also provides a predictive framework for anticipating the effects of solid-state bonding.
According to Mostafa Hassani, a senior author and assistant professor in the Sibley School of Mechanical and Aerospace Engineering and the Department of Materials Science and Engineering, "This marks a paradigm shift in our understanding of the process-microstructure-property relationships in impact-induced bonding." These findings could lead to more reliable and performance-oriented designs for surface modifications, repairs, and new additive manufacturing technologies that capitalize on supersonic impact bonding.
One of the major advantages of supersonic 3D printing technology—often referred to as "cold spray"—is its ability to produce materials without the need for heat or melting, which ultimately yields superior mechanical properties compared to traditional manufacturing techniques. This capability makes it especially valuable for critical structural applications in aerospace, energy sectors, and beyond.
To achieve solid-state bonding, the researchers devised a laser-induced launch platform that could accelerate micrometer-sized aluminum particles to speeds exceeding 2,200 miles per hour. Following the collisions, micromechanical tensile testing with a scanning electron microscope directly measured the strength of the bonds across different points of the impact interface.
Interestingly, the study revealed that bond strength is not uniform; it varies dramatically from the center to the edges of the impact site. Specifically, the center exhibits a weaker bond, but bond strength increases rapidly to a peak before plateauing toward the outer edges. A pivotal discovery was how the form of the native oxide present at the interface—whether in the form of layers, particles, or debris—affects local bond strength. Areas with scattered oxide debris demonstrated significantly stronger bonds compared to regions where the oxide layer remained mostly intact.
To further elucidate these variations in bond strength, the team established a predictive model that incorporates two critical parameters: contact pressure and surface exposure. As a microparticle collides with the substrate, the shear forces fracture the oxide layer, exposing more metallic surface. This newly revealed surface is then subjected to pressure that fuses it at an atomic level, resulting in a strong bond.
The implications of this groundbreaking research extend beyond enhancing bond strength. As Qi Tang, a doctoral student and lead author of the study, pointed out, "This understanding opens up new possibilities for tailoring interfacial properties and designing impact conditions—such as selecting materials, adjusting particle size, velocity, and temperature—to improve bonding and interfacial strength." In addition, insights from this study could be instrumental in preventing unwanted bonding, such as through the engineering of surface structures to protect against contamination from supersonic space dust impacts on spacecraft shields or telescope lenses.
This remarkable research not only propels forward the field of material science but also paves the way for future advancements that could reshape manufacturing and engineering as we know it! Stay tuned for more updates on these fascinating developments!