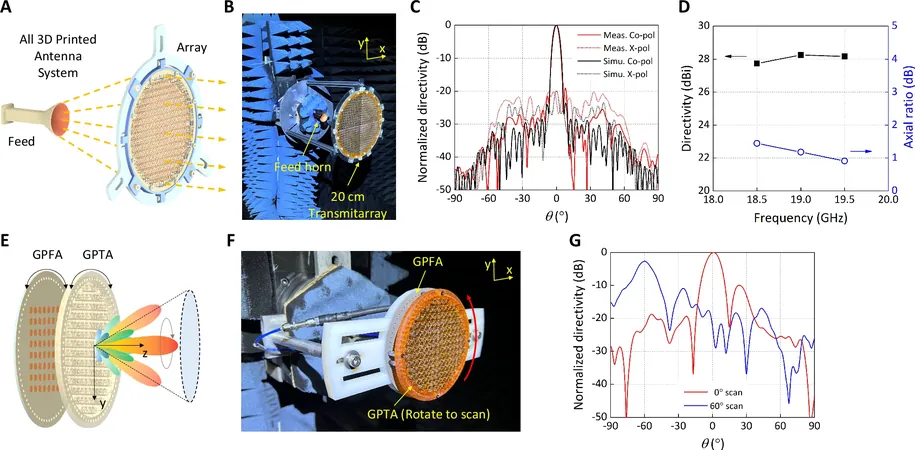
Revolutionary 3D Printed Antennas Slash Weight by 94%: The Future of High-Frequency Technology!
2025-06-17
Author: Liam
A Collaborative Breakthrough in Antenna Technology
A groundbreaking collaboration between the University of California, Berkeley, UCLA, and Lawrence Berkeley National Laboratory has birthed a game-changing method for 3D printing ultralight, high-frequency antennas! Published in the prestigious journal *Nature Communications*, this innovative approach employs a charge-programmed deposition process that combines conductive and dielectric materials in a revolutionary way, completely eliminating the need for substrates and sintering.
An Unbelievable Weight Reduction!
Imagine an antenna weighing a mere 5 grams—over 90% lighter than traditional counterparts! This astonishing reduction was achieved through testing antennas at 19 GHz, including circularly polarized transmitarrays and advanced horn feeds with internal waveguide structures.
How It Works: The Science Behind CPD
The charge-programmed deposition (CPD) technique fuses the precision of stereolithography with charge-guided material deposition. By applying electrostatic polarities to photo-curable resins, engineers have ingeniously directed metal ions during electroless plating, enabling substrate-free 3D printing that boasts interwoven dielectric and metallic features without any post-sintering hassle.
Impressive Measurements Validate Performance
Rigorous testing at UCLA showcased the remarkable efficiency of the printed antennas, achieving performance within just 0.8 dB of simulated projections. The DP process empowers researchers to produce a plethora of antenna types—including Vivaldi antennas, compact folded antennas, and sophisticated horn structures—all fully integrated without the need for additional substrates.
Material Flexibility: The Key to Innovation
The technology is not limited to standard materials. Researchers have successfully adapted polyimide, epoxy thermosets, elastomers, and ceramic composites for CPD use. One experimental patch antenna even utilized liquid metal eutectic gallium-indium as a conductive interface, demonstrating exceptional adaptability in design.
Unifying Form and Function
The researchers' designs effectively meld performance with minimal weight. A 12 cm transmitarray included three precise copper S-ring elements per unit cell, embedded within a cleverly designed dielectric skeleton that maintained air gaps for better performance. The result? Outstanding electromagnetic functionality combined with stunning lightness!
Innovation Meets Scalability
Navigating the limitations of traditional desktop systems, the team adopted a clever modular tiling strategy, producing a larger 20 cm transmitarray from four individually printed quadrants. Testing confirmed its stellar performance, achieving a measured directivity of 28.3 dBi at 19 GHz—almost identical to the 29.1 dBi predicted by simulations!
The Future is Bright, and Light!
These revolutionary fabrication techniques not only allow for the creation of multiple device types in a single workflow but also dramatically reduce weight—paving the way for new form factors in antenna design. Made entirely using commercially available desktop systems, this approach marks a significant leap forward in the field of 3D printed antennas.
Looking Towards Tomorrow
As the world of technology races forward, this innovative charge-programmed deposition method is set to redefine the limits of what’s possible in antenna design. With applications ranging from telecommunications to advanced aerospace technologies, the future of ultralight antennas is here—lighter, smarter, and more efficient than ever.
Stay tuned as we uncover more stunning advancements in 3D printing and antenna technology!