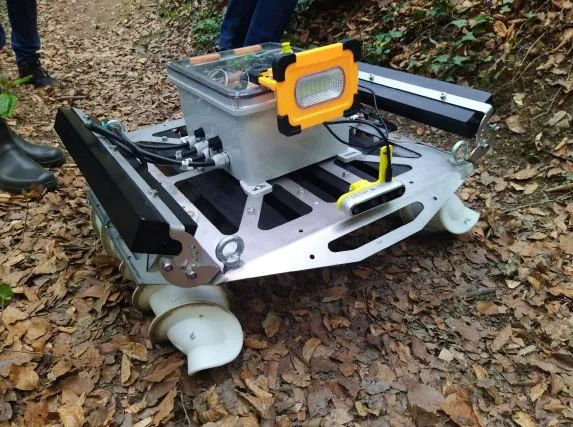
The Future of Space Exploration: A Screw-Driven Robot Could Transform Mining on Rocky Worlds!
2024-11-13
Author: Rajesh
Introduction
Exploring the rough and rocky terrains of celestial bodies has been one of the significant obstacles for space missions. Recent attempts, such as NASA's Free Spirit rover on Mars, faced considerable challenges, including unsuccessful efforts to extract it from difficult ground. However, a new frontier in autonomous exploration may have been opened thanks to innovative engineering. A team of researchers in the European Union has developed a groundbreaking mining robot powered by Archimedes screws, promising improvement in navigating these harsh landscapes.
Prototype Testing and Design
This new miniaturized mining robot is already undergoing rigorous testing, with prototypes proving effective on a variety of surfaces. The latest research paper released by the team highlights a versatile mobility platform utilizing four independently controlled Archimedes screws, which not only aids in mining operations but could be applied in numerous environments beyond just resource extraction.
Engineering Innovations
Much of this project began with the development of computer models, paving the way for a Computer-Aided Design (CAD) prototype that was meticulously tested across different terrains. While using an Archimedes screw for propulsion has faced scrutiny regarding efficiency in certain conditions, its ability to traverse nearly all types of surfaces makes it a strong contender in robotic exploration.
Kinematics and Control
The engineering team focused heavily on kinematics—how the robot moves and responds—by creating a detailed model that helps coordinate the four screws. Thanks to advanced control algorithms onboard the robot, each screw can be aligned effectively to maneuver the robot in the desired direction.
Sensor Integration
To further enhance its capabilities, the team integrated a sophisticated network of sensors. These sensors include time-of-flight positioning systems that allow the robot to measure distance, as well as force sensors that prevent the screws from overworking and damaging their motors. This sensor network is essential for the robot to understand its orientation in the field, ensuring operational efficiency and safety.
Prototype Construction and Testing
After drafting the preliminary control code, the team constructed a physical prototype, incorporating advanced 3D printing technology. In testing scenarios that included traversing snow, sand, frozen ground, and mud, the robot performed admirably on flat terrain. While it excelled in straightforward conditions, adapting to steeper slopes and more complex terrain will require further development.
Future Prospects
The EU project ROBOMINERS is currently refining this autonomous mining robot, with hopes of finalizing its prototype soon. The encouraging results from the recent terrain testing indicate that this technology could one day play a pivotal role in lunar and Martian exploration efforts, potentially revolutionizing how we approach resource harvesting beyond Earth.
Conclusion
Are we on the brink of a technological breakthrough that could change our understanding of mining off-planet? Stay tuned as the world watches these innovative robotic advancements!