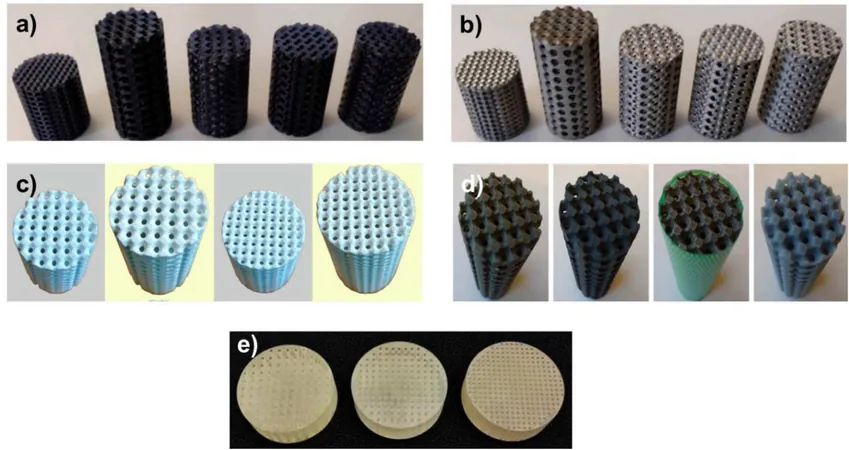
Revolutionizing Sound: How 3D Printing is Transforming Acoustic Metamaterials
2025-05-22
Author: Wei
Unlocking New Acoustic Possibilities
Imagine a world where sound is controlled with surgical precision—thanks to recent insights from a review published in *Virtual and Physical Prototyping*, this vision is coming to life through the burgeoning field of additively manufactured acoustic metamaterials. Jointly authored by innovators from Khalifa University and Dassault Aviation, the study highlights a groundbreaking transformation in sound management through 3D printing , paving the way for enhanced sound absorption techniques tailored for various applications.
3D Printing: The Game-Changer in Acoustic Engineering
Additive manufacturing provides a unique toolkit for engineers and researchers, allowing them to meticulously craft the geometry, material distribution, and internal framework of acoustic metamaterials. This level of customization empowers designers to fine-tune sound behavior for specific frequency ranges, all while optimizing weight and structural integrity.
Contrasting sharply with traditional sound-absorbing materials—like porous foams and fibrous panels—3D printing breaks past the limitations of fixed properties. Designers can fabricate resonant structures and intricate internal cavities with unparalleled precision, giving them ultimate control over how sound waves engage with materials.
The Evolution of Acoustic Absorbers
The review categorizes acoustic metamaterials into four structural families—each with distinct mechanisms for sound management. Perforated metamaterials utilize energy-dissipating micro-holes to absorb mid- to high-frequency noise, enhanced via underlying air cavities for greater low-frequency performance. Slotted designs, with their complex pathways, extend the acoustic journey, providing effective low-frequency attenuation in compact configurations.
Cellular structures, including honeycombs and gyroids, are meticulously engineered for broad-spectrum performance using controlled porosity, while hybrid designs cleverly merge features from different families for tuneable, wideband absorption across various acoustic landscapes.
Validation and Future Directions
Experimental validation solidifies the efficacy of these innovative metamaterials, using established metrics like the sound absorption coefficient (SAC), measured through precise testing methods like impedance tubes and reverberation chambers. Remarkably, even minor tweaks—like altering perforation angles or adjusting cell density—can significantly enhance performance, reinforcing additive manufacturing's pivotal role in acoustic engineering.
Looking to the future, exciting technologies such as volumetric 3D printing, multi-material processes, and even 4D printing with smart materials hold promise for creating adaptable sound absorbers that evolve with environmental changes.
The Increasing Interest in 3D-Printed Acoustics
Interest in the acoustic potential of 3D printing has surged recently. In 2019, researchers from the University of Sussex unveiled a 3D printed metamaterial capable of directing sound to specific locations, highlighting how this technology could reshape personal audio experiences. The University of Strathclyde is also making strides with a £500,000 initiative aimed at developing miniaturized, high-performance acoustic systems using 3D printing.
Notably, brands like Campfire Audio are already capitalizing on additive manufacturing to fine-tune earphone structures for improved sound quality and comfort. Meanwhile, experimental avenues are being explored, such as using sound itself to aid fabrication, as demonstrated in studies on holographic Direct Sound Printing (DSP), which captures ultrasonic fields to solidify materials.
The Future is Here: 3D Printing Meets Acoustic Innovation
These developments not only underscore the exciting convergence of 3D printing and acoustic technology but also herald a new era for engineered sound-absorbing metamaterials. The future looks bright for innovations that promise to redefine our relationship with sound.