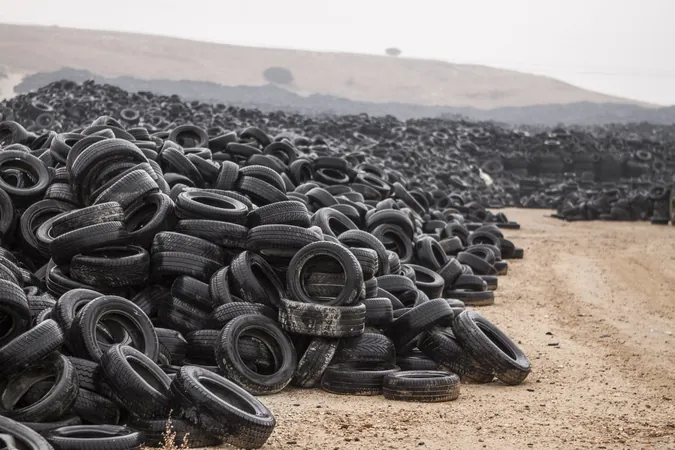
Revolutionizing Rubber Recycling: The Sustainable Solution We’ve All Been Waiting For!
2025-03-27
Author: Nur
In the battle against rubber waste, a new ray of hope has emerged. Every year, millions of tyres are discarded, significantly contributing to our ever-worsening climate crisis. In 2021 alone, the United States saw over 274 million tyres thrown away, with nearly 20% landing in landfills. This not only occupies precious space but also poses serious environmental threats through chemical leaching and the danger of spontaneous combustion.
The Dangerous Legacy of Traditional Methods
While pyrolysis, a method that chemically decomposes rubber, has been employed to recycle tyres, it’s not without its drawbacks. This process can release harmful byproducts such as benzene and dioxins, raising alarming questions about human health and environmental safety. With conventional recycling techniques struggling to effectively decompose rubber’s complex structure, alternative solutions are desperately needed.
A Breakthrough from North Carolina Researchers
Enter a pioneering study from the University of North Carolina at Chapel Hill, led by Dr. Aleksandr Zhukhovitskiy. This groundbreaking research introduces a novel chemical process that breaks down rubber waste, converting it into valuable materials that have significant industrial potential. Key to this innovation is the ability to overcome the major hurdle of rubber recycling: the tightly cross-linked polymer chains that give rubber its durability but also render it difficult to recycle.
Most existing methods focus on breaking these sulfur cross-links or cleaving the polymer backbone, often leading to low-quality byproducts. However, the new technique introduces a sulfur diimide reagent that strategically attaches amine groups to the polymer chains, setting the stage for a radical transformation of the rubber’s structure.
From Waste to High-Value Products
This new process results in a soluble material that maintains valuable functional properties, enabling the repurposing of rubber into high-end products such as epoxy resins. These resins, essential in various industries from adhesives to coatings, are traditionally derived from petroleum-based sources. However, researchers have demonstrated that their innovative method can produce resins with comparable strength to those made from fossil fuels. This discovery not only offers a sustainable alternative to traditional resin sourcing but also significantly reduces dependence on petroleum, thus mitigating its environmental impacts.
Mild and Eco-Friendly Process
What’s more impressive is that this new method operates under mild conditions, typically requiring temperatures between 35-50°C (95-122°F) in water-based environments. This approach minimizes the use of harmful solvents, making it both cost-effective and environmentally friendly—a far cry from conventional methods that often require high temperatures or expensive catalysts.
Assessing Environmental Impact
To gauge the sustainability of their process, the research team utilized the Environmental Impact Factor (E-factor), which evaluates waste produced in relation to valuable product yield. Although the overall E-factor—including solvents—was high, the simple E-factor (excluding solvents) proved much lower, indicating that there’s room for further optimizations to enhance sustainability and reduce waste generation.
A Game-Changer for Rubber Recycling
This innovative method presents a transformative approach to handling post-consumer rubber waste, aiming to convert what was once destined for landfills into valuable industrial materials. With the research team actively exploring greener solvent systems and optimizing reaction conditions, the potential for even more sustainable outcomes lies ahead.
As we stand on the precipice of a more eco-friendly future, it’s clear that this breakthrough will not only help address one of our planet's pressing environmental challenges but also pave the way for the recycling industry’s evolution. Buckle up, because this could very well be the game-changer we've all been waiting for!