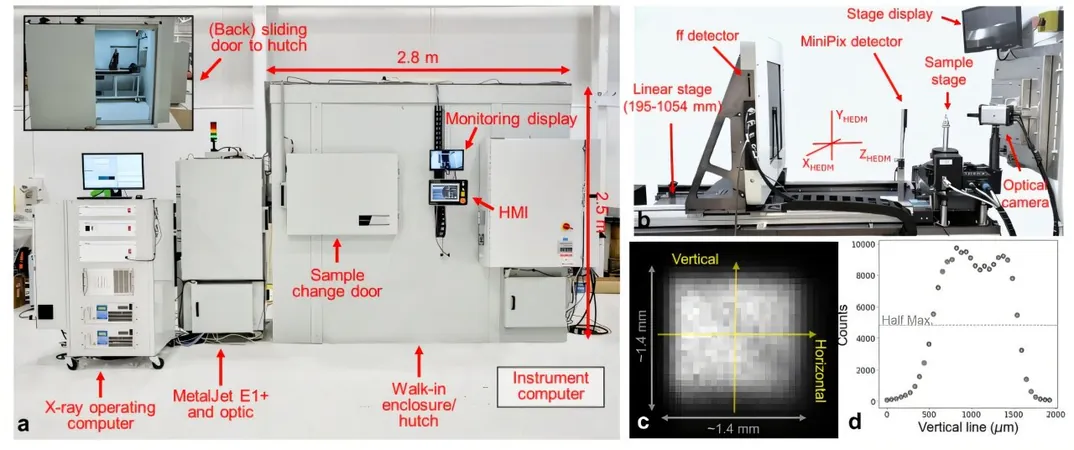
Revolutionizing Material Science: Tiny Synchrotron Brings Big Advances in 3D X-ray Microscopy to Local Labs
2025-04-29
Author: Jia
A groundbreaking innovation is set to transform the way researchers analyze materials. For the first time ever, scientists can now explore the intricate microstructures of metals, ceramics, and rocks right in their standard laboratories—eliminating the need for a trip to expensive and inaccessible particle accelerators.
This pioneering work, led by engineers at the University of Michigan, is detailed in the prestigious journal Nature Communications. The newly developed technique, dubbed 3D X-ray diffraction (3DXRD), opens the door for rapid analysis of samples in both academic institutions and industrial settings. This leap can significantly enhance the educational opportunities available for students as well.
How 3DXRD Works: A Game Changer for Material Analysis
3DXRD functions similarly to a CT scan, creating detailed 3D images from X-rays captured at various angles. Unlike a CT scan which revolves around a patient, in this case, the tiny material sample, just a few millimeters across, rotates in front of an ultra-powerful beam—delivering about a million times more X-ray intensity than a conventional medical X-ray. This incredible concentration of X-rays allows researchers to capture micro-level images of the tiny fused crystals that constitute most metals, ceramics, and rocks, known collectively as polycrystalline materials.
With this advanced imaging capability, scientists can assess how materials respond to mechanical stresses by accurately measuring the volume, position, orientation, and strain of thousands of individual crystals. For instance, examining a steel beam under compression can reveal how each crystal handles the immense weight of a building, paving the way for insights into large-scale wear and tear.
From Synchrotrons to Your Lab: No More Long Waits!
Historically, synchrotron facilities have been the only places equipped to provide the intense X-ray beams necessary for 3DXRD research. However, with only around 70 such facilities globally, researchers often face long wait times for access—sometimes taking two years just to secure a handful of experimental days.
In a bold move to democratize this technology, the research team collaborated with PROTO Manufacturing to develop the first compact, laboratory-scale 3DXRD unit. Remarkably, this entire instrument is about the size of a standard residential bathroom and has the potential to be shrunk down to the dimensions of a broom closet!
Ashley Bucsek, U-M assistant professor and co-corresponding author of the study, expresses her excitement: "This technique delivers such fascinating data that I wanted to make opportunities available for high-risk, high-reward experiments without the pressure of waiting for synchrotron beam time. It opens up countless pedagogical moments for students, free from the anxiety of limited experiments."
Setting a New Standard: Accurate Results Without the Hassle
Previously, smaller devices struggled to produce sufficient X-rays due to the risk of melting the anode, where electrons collide to generate X-rays. The newly designed Lab-3DXRD utilizes a liquid-metal-jet anode that remains liquid at room temperature, significantly boosting power intake and X-ray production.
To validate their design, researchers tested the Lab-3DXRD by examining a titanium alloy sample through three distinct methods: Lab-3DXRD, synchrotron-3DXRD, and laboratory diffraction contrast tomography (LabDCT). The results were promising, with 96% accuracy in matching the results from the other two techniques—particularly excelling with larger crystals.
A Bright Future for Material Science
With the implementation of this in-house technique, Bucsek and her team can now conduct a multitude of new experiments and refine parameters in preparation for larger synchrotron studies. Bucsek compares the Lab-3DXRD to a backyard telescope, while synchrotron-3DXRD is likened to the Hubble—each has its unique uses, but now researchers are better equipped for significant experiments before venturing into the larger facilities.
The Lab-3DXRD also enables projects to extend beyond the traditional six-day synchrotron limit, which is especially beneficial for studying cyclic loading—how materials endure repeated stresses over thousands of cycles. The future of material research looks brighter than ever!
Seunghee Oh, who was a research fellow during the study, now continues her work at the X-ray Science Division at Argonne National Laboratory. The collaboration with PROTO Manufacturing highlights a collective effort in advancing material science through pioneering technologies.