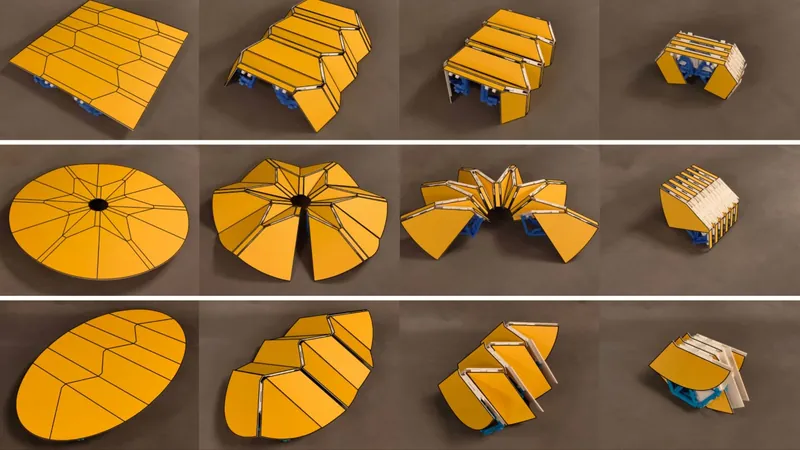
Revolutionizing Deployable Structures: The Future of Seamless Origami Engineering
2025-05-30
Author: Mei
Unfolding Innovation: Seamless Origami for Real-World Applications
A groundbreaking study published in *Nature Communications* introduces a revolutionary method for creating deployable structures that transform from compact origami folds into expansive surfaces without any visible seams. This innovation could revolutionize how we approach aerospace, emergency services, and medical equipment.
The Challenge of Thick Materials
While origami-inspired designs have garnered attention for their compact functionality, applying these techniques to thick materials poses a significant challenge. When materials are thick, the very folds that enable their transformation can conflict with each other, leading to complications in movement and structural integrity. Traditional thick-panel origami often falls short because it introduces valleys and gaps in crucial areas, rendering them ineffective for applications requiring continuous surfaces.
Tackling a Long-Standing Issue
This innovative research, spearheaded by Rui Peng from the National University of Singapore and Gregory S. Chirikjian from the University of Delaware, aims to eliminate this fundamental flaw. Prof. Chirikjian explained, "Current methods often complicate designs or fail to maintain seamless surfaces. Our goal is to significantly broaden the applications of thick origami by overcoming these constraints."
Innovative Panel Removal
The researchers adopted an unconventional approach that defies traditional engineering: rather than adding materials, they removed specific panels. By creatively disconnecting a middle panel between two side panels, they were able to close the gaps created during deployment.
This method proves effective as the origami structure is intentionally overconstrained, allowing for fewer elements while retaining essential functionality. Achieving this involves adhering to strict geometric principles.
Geometric Constraints for Movement
The strategy consists of two pivotal steps. First, it relies on a rigid origami tube satisfying symmetrical geometric conditions. Next, after panels are selectively removed and adjacent ones extended, there are precise extensions based on the thickness of the remaining panels.
Through a rigorous mathematical lens, the researchers ensured that the structures maintained their intended folding capabilities while eliminating gaps.
Versatile Designs for Diverse Applications
Demonstrating the adaptability of their design method, the researchers were able to create deployable structures across varying geometries. This flexibility indicates that their innovations could lead to applications in large-scale architecture—think deployable stadium roofs, efficient waterproof systems, and even space observatories.
At the consumer level, these designs could enhance convertible vehicle mechanisms or be scaled down for advanced soft robotics in medical surgeries.
A Methodology for the Future
Prof. Chirikjian remarked, "We have laid down a flexible methodology for constructing deployable structures, adaptable across numerous scenarios." The team also streamlined the design by reducing the number of top panels, easing the fabrication process while ensuring performance.
Prototypes and Future Directions
By developing 3D-printed prototypes, the researchers validated that their designs not only fold with remarkable efficiency but also expand into perfectly smooth surfaces. The innovations feature seamless yellow top surfaces, supported by robust blue structures underneath.
Prof. Chirikjian emphasized, "Material flexibility plays a crucial role, allowing various options; however, the methods of fabrication and assembly are vital for achieving high structural performance, especially given the many interconnected joints involved."
This research is a monumental step toward realizing smooth, uninterrupted surfaces that could unlock new possibilities in engineering for a multitude of real-world applications.