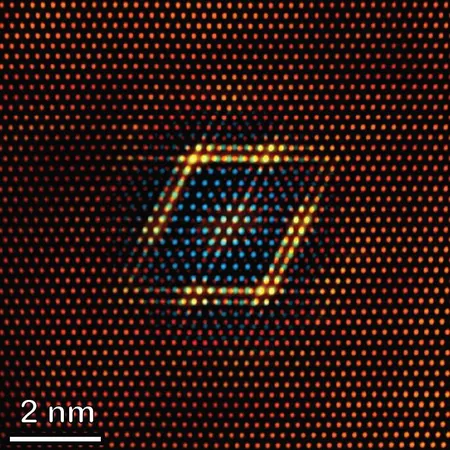
Revolutionary Copper Alloy Set to Transform Aerospace and Defense Industries with Unmatched Heat Resistance!
2025-03-29
Author: Sarah
Revolutionary Copper Alloy Set to Transform Aerospace and Defense Industries with Unmatched Heat Resistance!
In a masterpiece of scientific innovation, a groundbreaking nanostructured copper alloy named Cu-Ta-Li (Copper-Tantalum-Lithium) is emerging as a game-changer for high-temperature applications in aerospace, defense, and various industrial sectors. This remarkable material uniquely fuses the beneficial properties of several metals into an unprecedented hybrid solution.
Created through a partnership between the U.S. Army Research Laboratory (ARL) and Lehigh University (LU), the Cu-Ta-Li alloy stands out as one of the toughest copper-based materials ever developed. Its strength and thermal stability are thanks to contributions from renowned institutions like Arizona State University and Louisiana State University, helping to solidify its potential impact.
Cutting-Edge Material Science at Its Finest
“This is cutting-edge science; we are developing a new material that combines copper’s excellent conductivity with strength and durability comparable to nickel-based superalloys,” stated Martin Harmer, a co-author from Lehigh University. This revolutionary alloy is poised to provide both the military and various industries with newfound capabilities for hypersonic technologies and high-performance turbine engines.
At the heart of this innovative material is a technique pioneered at Lehigh University that employs a tantalum-rich atomic bilayer complexion. This complex structure plays a crucial role in stabilizing the nanocrystals, significantly reducing the risk of grain boundary destabilization under high temperatures. It allows Cu-Ta-Li to maintain its integrity even when pushed close to its melting point, greatly enhancing material performance during extreme thermal conditions.
Uniting Desirable Properties for Next-Gen Applications
The Cu-Ta-Li alloy successfully amalgamates two critical traits: nickel’s robust thermal properties and copper’s superior electrical conductivity. While nickel has traditionally been used in jet engines due to its strength, it falls short on conductivity. On the other hand, tungsten is often recognized for its heat resistance but is hampered by density and brittleness issues during manufacturing.
This fusion of properties paves the way for revolutionary advancements in heat exchangers, propulsion systems, and heat management technologies that could be pivotal for missiles and hypersonic vehicles. Although Cu-Ta-Li will not entirely replace existing alloys, it is set to be a key complement in targeted engineering applications.
A Comprehensive Approach to Research and Development
The research team utilized a sophisticated combination of powder metallurgy and high-energy cryogenic milling to synthesize the alloy’s nanostructure. They then conducted extensive practical testing, including 10,000 hours of steady heating at 800°C, to evaluate the alloy’s long-term thermal resistance. Creep resistance experiments helped further establish how the material would perform under extreme conditions. Advanced computational models were employed to confirm the stabilizing properties of the tantalum bilayer structure through density functional theory.
As it stands, the U.S. Army Research Laboratory holds the patent for this groundbreaking alloy. Moving forward, the research team intends to assess the thermal conductivity of Cu-Ta-Li for in-depth comparative studies and aims to extend their innovative techniques to develop additional heat-resistant alloys.
“This project exemplifies the significant role of federal investments in fundamental science and how they bolster American leadership in materials technology,” noted Harmer. “Discoveries like this are essential for enhancing national security and driving industrial innovation.”
Look out for the paper titled "A High-temperature Nanostructured Cu-Ta-Li Alloy with Complexion-stabilized Precipitates," expected to make waves in the science community when it publishes on March 28, 2025, in the esteemed journal *Science*. The future of materials science is here, and it’s hotter and stronger than ever before!