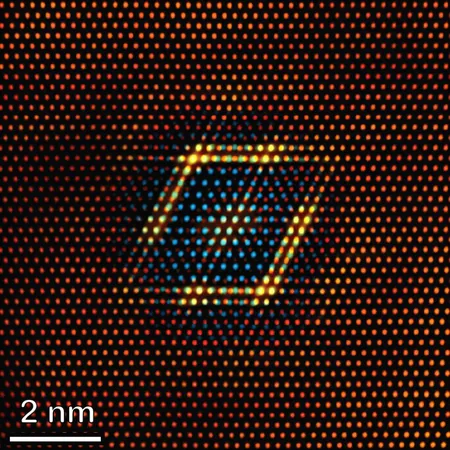
Revolutionary Copper Alloy Set to Transform Aerospace and Defense Industries
2025-03-27
Author: Rajesh
In an exciting scientific breakthrough, researchers from the U.S. Army Research Laboratory (ARL) and Lehigh University have unveiled a groundbreaking nanostructured copper-tantalum-lithium (Cu-Ta-Li) alloy. This innovative material promises to challenge the dominance of conventional superalloys, thanks to its remarkable thermal stability and mechanical strength, making it ideal for high-temperature applications in aerospace, defense, and industry.
Published in the prestigious journal *Science*, this discovery heralds a new era in material science. "This cutting-edge science is developing a new material that uniquely combines copper's excellent conductivity with strength and durability rivaling that of nickel-based superalloys," stated Martin Harmer, Alcoa Foundation Professor Emeritus of Materials Science and Engineering at Lehigh University. Such advancements could revolutionize the industry and military sectors by providing robust materials suitable for hypersonics and high-performance turbine engines.
Endurance Under Heat: The Alloy's Unique Properties
One of the most remarkable features of the Cu-Ta-Li alloy is its ability to withstand extreme temperatures without degrading. The researchers attribute this performance to the formation of Cu3Li precipitates, which are stabilized by a tantalum-rich atomic bilayer complexion. This groundbreaking concept prevents typical grain boundaries from migrating under heat, thereby maintaining the alloy’s nanocrystalline structure and improving its high-temperature performance.
Patrick Cantwell, a research scientist at Lehigh University and co-author of the study, emphasized the alloy's unique capabilities: "It holds its shape under extreme, long-term thermal exposure and mechanical stress, resisting deformation even near its melting point."
Paving the Way for Next-Gen Technologies
The implications of this new alloy are extensive. By merging the exceptional thermal resilience of nickel-based superalloys with copper's unparalleled electrical conductivity, the Cu-Ta-Li alloy opens avenues for advanced applications, including:
- **Heat exchangers** capable of operating in extreme environments.
- **Advanced propulsion systems** for aerospace crafts.
- **Thermal management solutions** essential for next-generation missile and hypersonic technologies.
Unlike traditional nickel-based superalloys that excel in durability but suffer from lower thermal conductivity, and tungsten-based alloys that are hard to manufacture due to their density, the Cu-Ta-Li alloy offers an ideal combination of strength, conductivity, and stability at extreme temperatures.
A Robust Research Journey
The team utilized advanced techniques, including powder metallurgy and high-energy cryogenic milling, to synthesize this robust alloy. Their rigorous testing regime included:
- Annealing for over 10,000 hours at 800°C to validate long-term stability.
- Advanced microscopy for analyzing the intricate structure of Cu3Li precipitates.
- Creep resistance experiments to ensure durability under stress.
In recognition of its innovative potential, the U.S. Army Research Laboratory has been awarded a patent (US 11,975,385 B2) for the Cu-Ta-Li alloy, underscoring its critical importance for defense applications, such as military propulsion systems and heat exchangers.
Looking Forward: Further Research and Development
Scientists behind this innovative material plan to delve deeper into direct measurements of its thermal conductivity and compare it with nickel-based alternatives. They also aim to develop more high-temperature alloys using similar design strategies.
"This project exemplifies how federal investment in fundamental science helps maintain American leadership in materials technology," Harmer noted. The breakthrough promises to enhance national security while sparking industrial innovation, marking a significant step forward in the quest for advanced materials that truly meet the demands of the future.
Stay tuned as this exciting development unfolds—it's a leap towards creating stronger, lighter, and more efficient materials that could change the face of various industries!