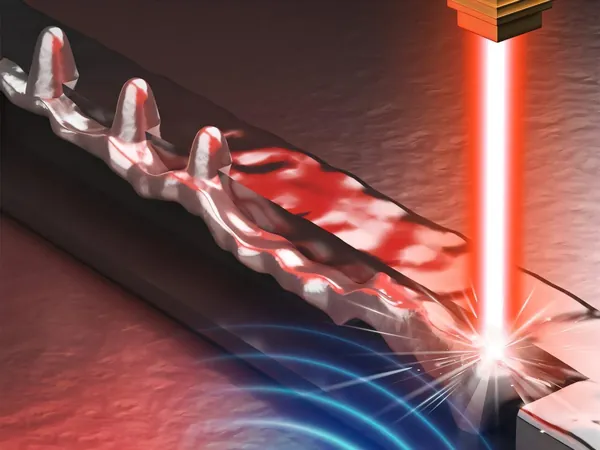
Revolutionary Breakthrough: Researchers Accelerate Laser Welding to Transform Fuel Cell Production!
2025-01-21
Author: Jia
In a groundbreaking development, researchers have significantly enhanced high-speed laser welding, a crucial process for the production of fuel cells, which are heralded as a clean energy solution for various sectors, particularly in eco-friendly vehicles. Fuel cells generate clean energy without emissions, making them a game-changer in the fight against climate change.
Traditionally, the challenge with laser welding for fuel cells has been the issue of "humping" – an unsightly deformation on weld seams that arises when the welding speed is excessively high. This defect has previously limited manufacturing speeds and production rates of vital components like bipolar plates, essential for efficient fuel cell operation.
The team at Penn State, spearheaded by professor Jingjing Li, has embarked on a quest to tackle this dilemma. Their research combines real-time observation with advanced analytical modeling, successfully identifying the conditions leading to humping during high-speed welding. Their findings, published in Nature Communications, reveal that critical adjustments in the welding process can facilitate faster production without compromising the quality of the welds.
"We sought to significantly enhance our welding speeds to boost the manufacturing rates of bipolar plates, which are integral to fuel cell energy generation," described Li. This innovation paves the way for an impressive increase, raising the maximum welding speed from just 20 meters per minute to an astounding 75 meters per minute.
Zen-Hao Lai, the first author on the paper and a doctoral student in Materials Science and Engineering, emphasized the impact of their work: "At this new speed, we can manufacture approximately 80,000 fuel cells each year, as each cell requires two welded bipolar plates." These plates, typically ranging in size from 8x8 to 12x12 inches, form critical channels necessary for the efficient generation of energy in fuel cells.
To achieve this milestone, the researchers employed cutting-edge synchrotron X-ray imaging, offering unprecedented insights into the welding process. By harnessing numerical simulations alongside their experimental data, they developed an equation to effectively link defects with specific welding parameters. One of their major discoveries was the need to stabilize molten metal pools during welding, which can be accomplished through simple adjustments like applying a shielding gas or modifying the laser beam’s shape.
By leveraging these newfound insights, the team successfully eliminated humping while maintaining a remarkable increase in production speed. "Our understanding of the relationship between humping and welding parameters enabled us to modify settings to achieve smoother, high-speed welds," stated Lai. The implications of this research not only enhance the fundamental understanding of laser welding technology but also resolve pressing manufacturing challenges.
Looking ahead, the researchers are committed to refining the welding process further to achieve even faster and defect-free results. Li notes, "This work pushes the boundaries of industrial and manufacturing engineering, showcasing a dynamic interplay between fundamental research and practical applications. It exemplifies how scientific insights can lead to innovative solutions in real-world manufacturing challenges."
As our world pushes toward sustainable energy solutions, advancements like these are vital in driving the future of fuel cell technology, promising a cleaner, greener tomorrow!