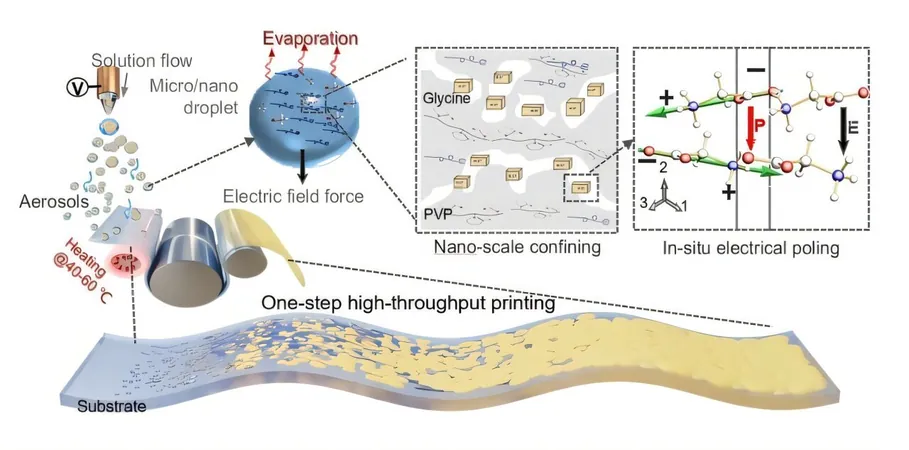
Revolutionary Aerosol Printing Technology Set to Transform Wearable Bioelectronics
2024-11-11
Author: Sarah
Introduction
In an era where the demand for bio-MEMS, wearable tech, and implantable medical devices is skyrocketing, researchers are racing to develop piezoelectric biomaterials. Recognized for their extraordinary electromechanical properties, biocompatibility, and bioresorbability, these materials hold great promise for future biomedical applications.
Historical Challenges
Historically, the field has faced enormous challenges, particularly in the precise manipulation of nano-biomolecules and controlling their structural growth from the nano-scale to larger forms. Since the intriguing discovery of biological piezoelectricity in materials such as wool and hair back in 1941, attempts to harness piezoelectric effects in biomaterials have largely faltered. For nearly 80 years, this issue has posed a significant barrier, leaving a gap between experimental biomaterials and their practical applications in bio-devices.
Breakthrough in Printing Technology
However, a remarkable breakthrough has been achieved by a research team at The Hong Kong University of Science and Technology (HKUST). They have unveiled an innovative thermal-electric aerosol (TEA) printing technology that allows for one-step, high-speed manufacturing of flexible piezoelectric biofilms. This pivotal research has been published in the esteemed journal Science Advances.
Advantages of TEA Printing
The TEA printer is designed for roll-to-roll printing, which dramatically enhances the production rate of piezoelectric films intended for a variety of uses, such as miniaturized bioelectronics and advanced therapeutic tissues. Not only does this method promise industrial-scale production capabilities, but it also combines the advantages of top-down additive manufacturing with bottom-up nano-biomolecule assembly to close the long-standing divide between theoretical biomaterials and functional bio-devices.
Speed and Efficiency
Traditional biomolecular assembly methods can take anywhere from 30 minutes to 48 hours, resulting in slow manufacturing processes and unwanted structural defects. In stark contrast, the TEA printer utilizes state-of-the-art electrohydrodynamic aerosolization and in-situ electrical poling techniques, achieving an impressive printing length of 8,600 millimeters per day—twice the speed of current techniques.
Performance of Biofilms
The glycine/polyvinylpyrrolidone films produced through this advanced printing process have demonstrated a piezoelectric voltage coefficient of 190 × 10⁻³ V·m/N, an astonishing tenfold increase compared to the standard lead zirconate titanate used in the industry. Furthermore, these biofilms exhibit nearly 100 times better mechanical flexibility than their glycine crystal counterparts.
Future Applications
The TEA printer's ability to work with a wide array of biomaterials, including chitosan and poly(L-lactic acid), paves the way for further expansion of its applications. The next steps in this research involve leveraging machine learning and existing libraries of piezoelectric biomaterials to accelerate the creation of a diverse range of materials optimized for flexible bioelectronics and therapeutic biomaterials.
Conclusion
This pioneering research not only highlights exciting advancements in biofabrication but also signifies a potential revolution in how we approach the design and manufacturing of cutting-edge wearable technologies and innovative healthcare solutions. The future of biomedical devices may be just a print away!