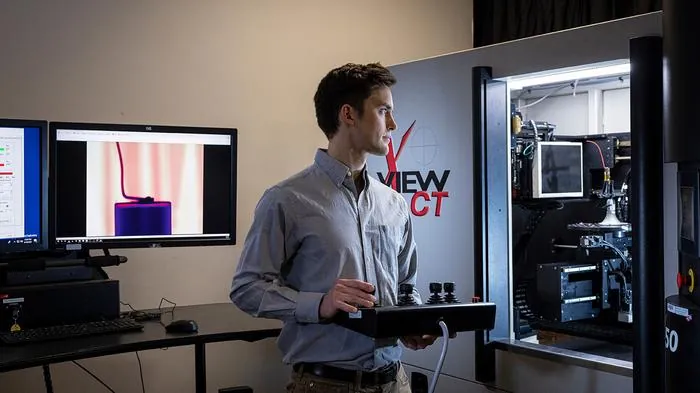
Revolutionary Advances in Titanium Alloys: How AI is Changing Additive Manufacturing Forever
2025-03-13
Author: Yu
Introduction
In an extraordinary leap forward for the field of materials science, researchers at Johns Hopkins University have harnessed artificial intelligence (AI) to significantly enhance titanium alloys, particularly Ti-6Al-4V. Their groundbreaking work utilizes powder bed fusion, leading to unprecedented improvements in production speed, material strength, and overall efficiency.
Challenges in Additive Manufacturing
Traditionally, the properties of parts created through additive manufacturing (AM) have varied greatly from those produced using conventional methods. Differences in microstructure have posed challenges in terms of reproducibility and certification. However, this very variability presents a golden opportunity for innovation.
Addressing Manufacturing Needs
Morgan Trexler, a program manager with the Applied Physics Laboratory (APL) at Johns Hopkins, articulated a pressing need: "The nation faces an urgent need to accelerate manufacturing to meet the demands of current and future conflicts." To address this challenge, the team is advancing research in laser-based additive manufacturing to expedite the development of mission-ready materials. This ensures production capabilities can keep pace with evolving operational needs across defense and aerospace sectors.
AI-Driven Discoveries in Processing
By employing AI-driven models, the research team explored previously uncharted manufacturing conditions for laser powder bed fusion (L-PBF). The revelations from their findings challenge long-standing beliefs about manufacturing process limitations. They uncovered a wider processing window for creating dense, high-quality titanium with custom-tailored mechanical properties.
Transformational Insights from AI
Brendan Croom, a senior materials scientist at APL, described the transformation, stating, "For years, we assumed that certain processing parameters were ‘off-limits’ for all materials due to potential quality degradation. However, AI has enabled us to probe the full spectrum of possibilities, unveiling new processing regions capable of faster printing without compromising — and even enhancing — material strength and ductility."
Broadening Industry Applications
The implications of this research extend beyond titanium itself. With the capability to produce stronger and lighter components at greater speeds, industries such as shipbuilding, aviation, and medical devices stand to benefit significantly. This approach is poised to redefine standards in aerospace and defense technology, contributing to a broader effort to elevate additive manufacturing practices.
Unlocking High-Density Processing Regimes
Not only does this previous machine learning approach uncover new avenues for titanium alloy production, but it also highlights a factor previously ignored: high-density processing regimes. These had been prematurely dismissed due to fears about material instability. Thanks to targeted adjustments in their methods, the team has successfully unlocked new pathways to process Ti-6Al-4V.
Breakthrough Achievements
Chief scientist Steve Storck emphasized the magnitude of this breakthrough, saying, "We’re not just making incremental improvements; we’re discovering entirely new ways to process these materials. In a remarkably short timeframe, we’ve identified processing conditions that push performance boundaries beyond what was previously thought possible."
Innovative Experimentation Methods
Gone are the days of manual adjustments in trial-and-error fashion. The research team utilized Bayesian optimization, a cutting-edge AI technique that forecasts the most promising subsequent experiment based on existing data. This iterative learning method allows for the exploration of thousands of configurations virtually before implementing a select few in the lab.
Balancing Production Factors
Instead of just speeding up production, the researchers advocate for striking the perfect balance among strength, flexibility, and efficiency. "AI is instrumental in guiding us to processing regions we wouldn’t have identified without this technology," Croom added.
Future Ambitions and Predictions
Moreover, the team's ambitions extend further still; they plan to expand their machine learning models to predict even more complex material behaviors. While initial work has focused on density, strength, and ductility, researchers are also keen to model other physical characteristics, such as fatigue resistance and corrosion.
Conclusion
"This research exemplifies the power of AI and data-driven manufacturing," Croom remarked. "In the past, it could take years to understand how new materials would behave in relevant environments. But what if we could condense that timeline to weeks? Imagine the potential for rapidly manufacturing enhanced alloys."
While this study centers on titanium, Storck confirmed that this innovative AI-driven approach is also being applied to other metals and manufacturing techniques, paving the way for customized alloys specifically engineered for additive manufacturing.
As the world of materials science evolves, the integration of artificial intelligence will undoubtedly fuel a new era of manufacturing efficiency and capabilities. This breakthrough signifies just the beginning of what can be achieved — and the future looks incredibly promising!