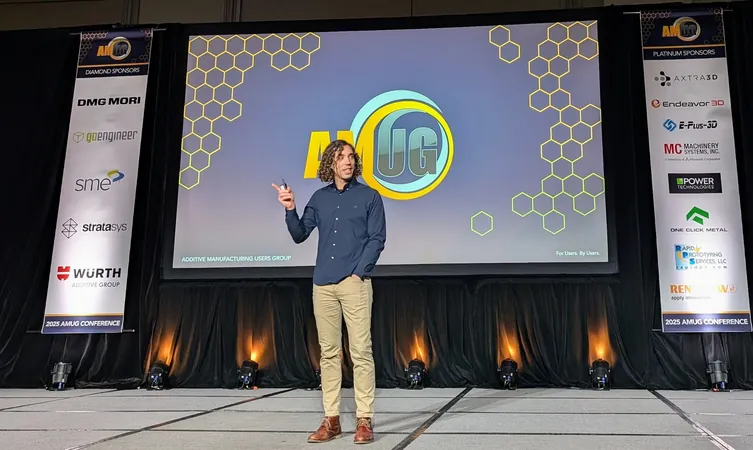
NASA's Ingenious Solution for Mars Missions: 3D Printed Crushable Lattices
2025-04-24
Author: Yu
Breaking New Ground with 3D Printing at NASA
NASA's Jet Propulsion Laboratory (JPL) is revolutionizing structural design and advanced manufacturing by integrating 3D printed crushable lattices into the Mars Sample Return mission. Led by mechanical engineer Ryan Watkins, this groundbreaking initiative combines state-of-the-art simulation tools with controlled additive manufacturing, addressing not just technical challenges but the intricate cultural dynamics within institutional framework.
Cultural Shifts: The Real Challenge Behind Innovation
The biggest hurdle wasn't the technical design of the lattices but rather gaining acceptance for this innovative technology in a major NASA mission. Watkins emphasized that trust and experience played vital roles during his initial years at JPL.
Redefining Impact Safety: Lattices to the Rescue
The Mars Sample Return mission faces a daunting reality: the return capsule will impact Earth's surface at speeds approaching 110 miles per hour without parachutes or propulsion. To ensure the safety of Martian samples collected by the Perseverance rover, Watkins' team is employing specially designed 3D printed crushable lattices, engineered to absorb impact energy.
The Path to Mars: How 3D Printing is Evolving
Additive manufacturing at JPL is no longer about just creating parts; it's about designing entire systems that harness the potential of these novel materials. With a history stretching back to the 1990s, JPL has continually pushed the limits of 3D printing, culminating in their innovative approach to the Mars Sample Return mission.
Simulating Success: The Role of Advanced Software
By utilizing the award-winning UnitcellHub software, Watkins’ team was able to model and test various lattice designs efficiently, narrowing down options to only two that met stringent structural requirements. This software empowers engineers to rapidly explore thousands of configurations, ensuring the selected design could withstand the extreme conditions of re-entry.
A Game-Changer for Future Missions
Watkins foresees that many future missions will incorporate more metal 3D printed parts. He believes that these advancements in engineering and production processes are what will ultimately ensure the success and reliability of space missions. The selected diamond-shaped lattice will serve as a critical protective barrier during the capsule's high-velocity descent.
Navigating the Technical Hurdles: From Research to Reality
Transitioning from theoretical prototypes to actual mission hardware is fraught with challenges. NASA’s Technology Readiness Level (TRL) framework often sees innovations falter between TRL 5 and 6. Watkins notes that the key to overcoming these barriers lies in effective communication and collaboration between researchers and engineers.
Preparing for the Final Countdown
As NASA gears up for the Critical Design Review (CDR) of the Mars Sample Return mission, the focus is now on finalizing the engineering processes necessary to manufacture the selected lattice structure. This innovative design promises to effectively protect precious geological samples during their tumultuous return to Earth.
A Call to Action for the Additive Manufacturing Community
Watkins concluded his presentation with an invigorating call to action for the broader AM community, urging his peers to shift their focus from mere demonstrations to utilizing the true engineering potential of lattice structures. His mission? To ensure that Martian samples return safely home—are you ready to join the revolution?