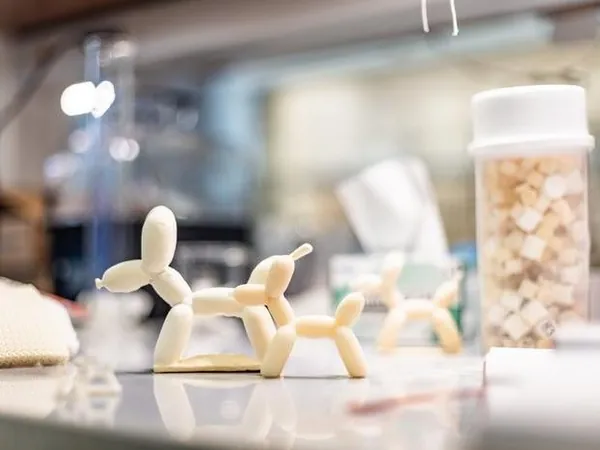
Breakthrough in 3D-Printed Foam Could Revolutionize Manufacturing!
2025-04-07
Author: Emily
Researchers from the University of Texas at Dallas have made a significant stride in the world of material science with a new 3D-printing formula that has the potential to revolutionize foam production. Their findings, published in the March 1 edition of *RSC Applied Polymers*, illustrate a method for creating lightweight yet sturdy foam using innovative 3D printing techniques. This method remains largely underutilized in commercial applications, as noted by co-lead author and doctoral student Rebecca Johnson.
"This project, spanning over two years, has been the most extensive undertaking of my academic journey," said Johnson, who is set to earn her PhD in chemistry this May. The challenge lay in perfecting the polymer formulation so it could be effectively utilized in 3D printing.
The researchers were able to create complex shapes, showcasing their proof-of-concept with a whimsical balloon dog design. This demonstrates not only the potential of 3D printing in producing customized materials but also addresses critical limitations associated with current polymer foam technologies.
According to Dr. Ron Smaldone, associate professor of chemistry and biochemistry, "One of the primary goals was to push the boundaries of what is achievable with 3D-printing polymer foams, especially for applications such as insulation and shock absorption." With additional research, this foam could find applications in safety products like motorcycle and football helmets, car bumpers, and even protective armor.
One of the key innovations in their research is the introduction of dynamic covalent chemistry, which allows for reversible bonding in the foam structure. While traditional thermoset foams undergo irreversible changes during production, meaning they cannot be reshaped or recycled, this new material can repair itself if damaged. This self-healing capability could lead to longer-lasting products and reduced waste in landfills—a major concern in today's environmental landscape.
Smaldone emphasized that they are not alone in their pursuit of advanced materials, but their use of dynamic chemistry to create exceptional foam sets their research apart. Looking ahead, the researchers are eager to explore how to fine-tune the properties of this foam for a variety of practical applications.
Co-lead author Ariel Tolfree, a fellow chemistry doctoral student, plans to delve deeper into the sustainability potential of the foam, working towards solutions that enhance its recyclability. "The choice to create a balloon dog was fitting," Tolfree explained. "It's a simple form that symbolizes the unseen potential of our foam. Like a balloon that can be transformed into something surprising, our foams invite curiosity and innovation."
This groundbreaking research represents a promising leap toward creating sustainable, versatile materials that not only meet the demands of modern manufacturing but also embrace environmental responsibility. Stay tuned as these innovative minds continue their quest to redefine the future of materials!